The Challenges of the ‘New Normal’
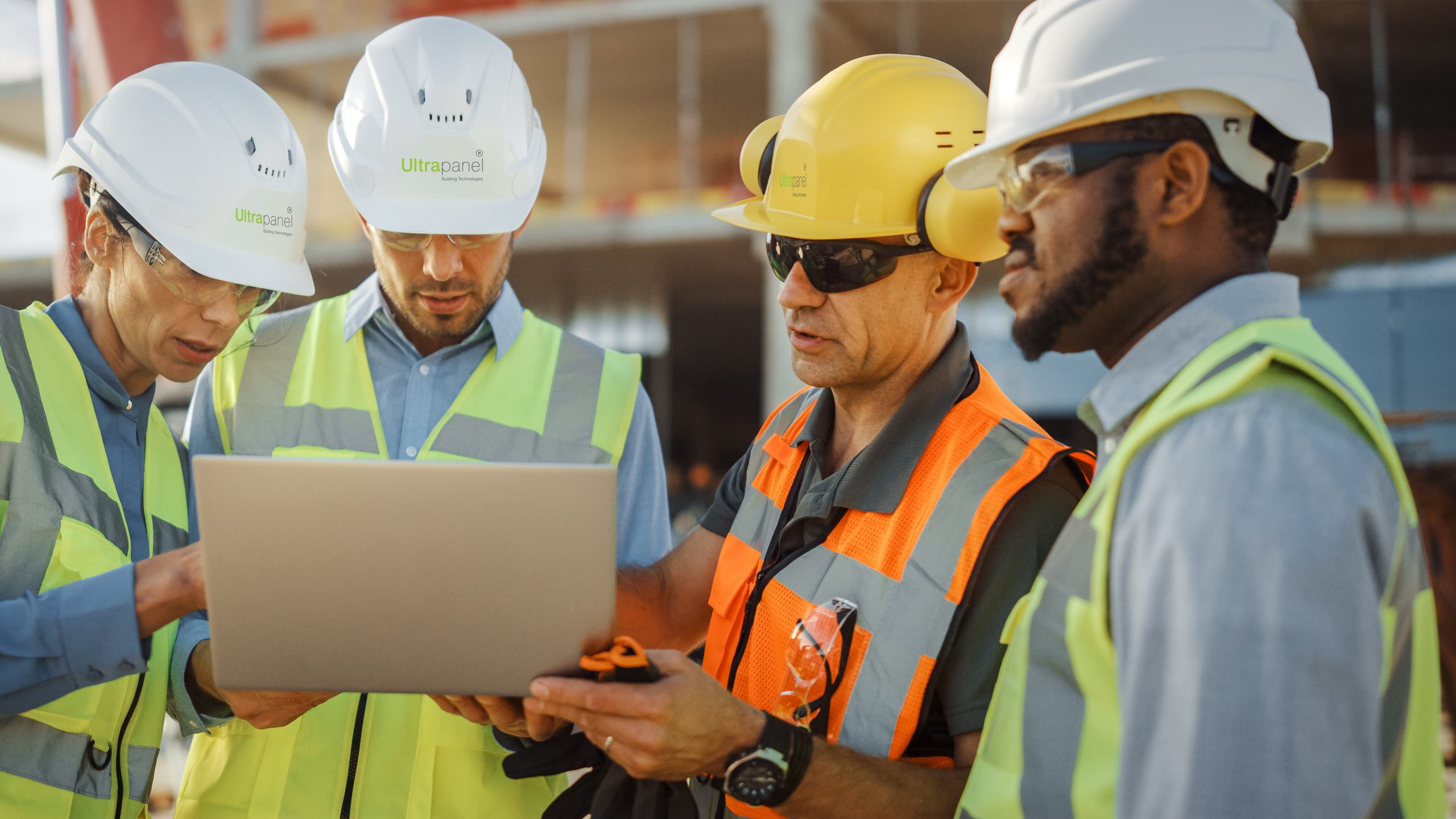
The pressure of operating Covid-secure construction sites combined with tough schedules, supply chain issues and difficult specification decisions are all taking a toll on housebuilders.
As we strive to recover and return to the ‘new normal’ with the challenges this presents – it is a given, at least in the short term – that social distancing measures are here to stay. There is now widespread agreement that in order to operate effectively and safely developers need to reduce their reliance on labour-intensive traditional construction methods and look to new advanced offsite approaches.
But it is clear there are more forces at play here – the Brexit-driven fear of a skills exodus, compounded by chaos in construction supply chains and materials shortages are also creating a climate for rapid change. Many are now realising that taking the construction process into well-managed factory environments where social distancing measures are easier to implement – is just one of a host of benefits.
Productivity or the lack of, has been an issue for the construction industry for decades. We have the skills and technology to overcome the pitfalls associated with traditional labour-intensive approaches, however some sectors have been slow on the uptake. The pandemic is changing this, and now offsite construction is becoming an increasingly dominant force.
It is not only construction methods that are going through a period of unprecedented transformation – working remotely has altered not only the way we use our homes but is also creating a change in consumer demand and maximising available space is now a priority.
Against this backdrop, in January 2021 Ultrapanel Building Technologies launched its next generation of ‘room in the roof’ systems that combine offsite techniques and advanced manufacturing technology. Tried and tested by one of the UK’s largest housebuilders, the system provides invaluable benefits for volume housebuilders not only looking to create space and increase revenue, but also to overcome supply chain concerns and eliminate complex performance and safety specification issues from the critical construction timeline.
The Ultrapanel ‘room in the roof’ system is both lightweight and easy to manoeuvre, reducing the cost and complexity of expensive lifting equipment and on-site cranage. The Ultrapanel system can be installed by a team of three with a telehandler in just one day to achieve a rapid weathertight building envelope. The adaptable system creates 50-60% more usable space than traditional attic trusses.
Importantly, windows and dormers can be placed anywhere in the roof with no ‘dead zones’. This means that the layout of the top floor room can be maximised as windows can be placed exactly where they are needed, even above staircases to bring natural light into the floors below. As Ultrapanel has no traditional roof trusses or purlins, the ceiling can be vaulted, allowing space for mezzanine floors in some roof designs.
“The complete Ultrapanel system is the only ‘room in the roof’ solution with BBA certification and NHBC Accepts,” says Andrew Thomson, Ultrapanel’s Design and Development Director. “This provides assurance to housebuilders that the structural, thermal, condensation and fire risk have all been independently verified. The design has a structural eaves section which distributes the load into the supporting walls, so the support traditionally required either side of a roof opening does not need aligning with the wall below. The absence of internal structure means maximum flexibility to utilise the space.”
Precision engineered in one ‘unitised hybrid panelised solution’ the Ultrapanel system maximises the material properties of the structural steel and timber elements, integrated with a high-performance insulated core. Mass customisation techniques at high capacity ensure simultaneous volume production of various roof types with vaulted ceilings, mezzanine floor options, and the ability to accommodate dormer or inline windows.
The Ultrapanel system is delivered to site as a complete ‘room in the roof’ kit of parts including all components and fixings at a pre-agreed assured price. Reducing the costs and risks surrounding on-site storage, means the system is more sustainable and eliminates onsite waste and associated disposal costs.
“We have been developing the system over the past four years alongside major housebuilders to ensure we get off to a quick start, says Andrew. “We have developed a version of the panel utilising non-combustible materials which we use for the party wall structure and we will continue to extend applications of this new material.”
With factory production taking just two weeks, Ultrapanel’s short lead time provides flexibility to housebuilders managing challenging and demanding schedules, and like all offsite technologies, reduces onsite frustrations such as poor weather and labour shortages. The pandemic combined with the Brexit transition has the potential to create serious challenges. With a two-week flexible lead time and an established supply chain, the Ultrapanel system can help volume housebuilders overcome the challenges of the ‘new normal’ and deliver critical time and space gains.